Equipment maintenance can be a high-risk activity
Running a business and taking care of everything is a demanding job. It requires a lot of sacrifice and time to make everything right in order for every part of the production process to run smoothly.
An important part of that production process is equipment that your company uses. Keeping track manually of all equipment services, breakdowns, employee training and equipment usage is time-consuming and unproductive.
How many times have you forgotten when is the next equipment service and that led to the breakdown of the same? We believe it cost you a lot more money than the service itself.
To avoid these and similar problems, your equipment should be organized so that at any time you can quickly access all the information about specific equipment. Wouldn’t that be great?
What if you had an overview of all the activities related to the equipment: who used the equipment, which employees are trained to work on the specific equipment, when is the next maintenance. That would save you a lot of time.
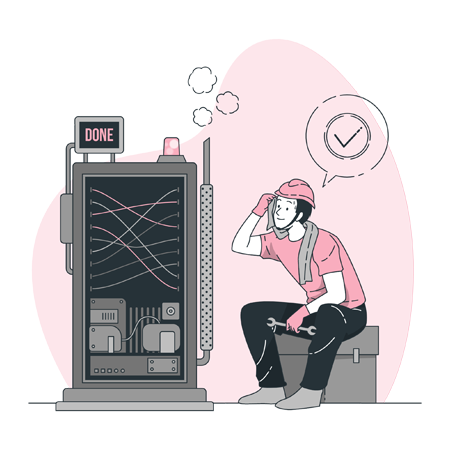
Asario software offers a number of options when it comes to your equipment.
Using the equipment in Asario, you have access to the following information:
- Current use of the equipment (which employee is currently using which equipment)
- Previous use of the equipment (which employees worked on the specific equipment)
- List of employees that are trained to operate specific equipment
- Equipment amortization cost
- Equipment groups (you can have an unlimited number of equipment within one group)
- Equipment information (serial number, manufacturer, warranty, etc...)
- Equipment past and future services
- List of operations for which specific equipment is used